It’s harvest season in the Northern hemisphere, so farmers head into the fields to gather the fruit of their hard labor. But now robots are along for the ride.
A few days ago, a boxy yellow robot rolled through the rows of yellow pepper patches in a Belgian greenhouse, spotting and picking the ripened fruit. Moving along the tall leafy plants, the robot paused whenever its camera detected a ripe yellow pepper and then with a quick move of a blade, cut the stem, grabbing the fruit with a palm-like catcher.
Named SWEEPER, the robot is a result of a collaboration between Israeli, Dutch, Swedish, and Belgian scientists—a complex piece of equipment aimed to help farmers and agricultural workers in the harvesting process. Peppers aren’t the only items SWEEPER should be able to handle. With some modification, similar robots can be devised to gather apples or tomatoes, for example.
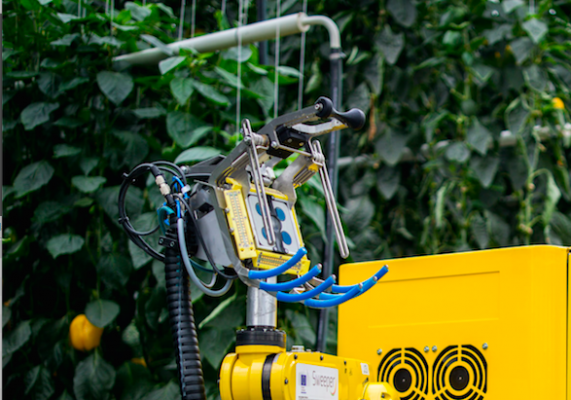
Some argue that these robots may cause job losses for agricultural workers, but the reality is more complex. As the climate changes, heat waves intensify, and humidity increases, working long hours in the field is becoming more unhealthy, and in some cases dangerous, for humans. Even greenhouse conditions, tailored to the plants’ needs, may in some cases be too hot or humid for people. According to reported data, from 1992 to 2006, 68 crop workers in the United States died from exposure to environmental heat. The Union of Concerned Scientists wrote that heat and drought are endangering the men and women who harvest nearly half of U.S.-grown fruits, nuts, and vegetables. In essence, toiling in the fields is a hard job that will become even harder as climate change progresses, so humans will likely have to rely on robots to do some farming. “We don’t expect these robots to replace people,” says Yael Edan, professor of Agricultural, Biological and Cognitive (ABC) Robotics at Ben-Gurion University in Israel, whose team worked on the SWEEPER robot. “We think they would help with tasks that are difficult for people to do.”
Want more stories like this one?
To teach SWEEPER to identify peppers and harvest them gently without damaging them or the plant they grew on required artificial intelligence and machine learning. Unlike humans, who can discern the colorful fruit among the green foliage quite easily, even in somewhat dim lighting, robots have a much more difficult time doing so. Ben-Gurion University’s roboticist Polina Kurtser says that the team had to use thousands of pictures of peppers to teach the robot to identify the vegetables. Lighting, which can change from one greenhouse to another or vary with the weather, and time of day can be a challenge too, says Boaz Arad, another team member.
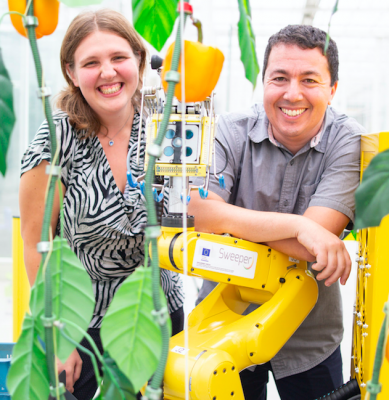
The harvesting arm, called a gripper or manipulator, went through many integrations, including pulling, cutting, dropping the fruit into a bag, and other harvesting variations—to devise the most efficient and safe model. “The part of the gripper that goes into the plant is very compact, it’s quite a smart design that prevents the knife from harming the plant,” Boaz says. It took the team about three and a half years to arrive at the current model, he adds. At the end, during its latest greenhouse demonstration, SWEEPER passed the test. The Ben-Gurion team is developing other agricultural innovations too. One of them is a smart pesticide sprayer that would calculate the exact amount of chemicals needed to keep plants healthy. Rather than spraying abundantly, the machine would target the chemicals, thereby reducing people’s exposure to them.
When will a team of SWEEPERS actually tend to pepper or tomato patches, whether in greenhouses or outdoors? The researchers are hoping this will happen soon. For example, Bogaerts, a supplier of greenhouse technology is interested in the product, Boaz says.